Fast-track hybrid testing platform for the development of battery systems
Efficient Li-Ion Battery Testing Solutions
Current methods for evaluating Li-ion batteries’ safety, performance, reliability, and lifetime entail significant resource consumption throughout the battery R&D process. Major considerations include the time or number of tests required, costly equipment, and a generalised trial-and-error approach. Additionally, there is a lack of understanding regarding the complex multi-scale and multi-physics phenomena within the battery system. Furthermore, testing facilities operate locally, meaning that data management is conducted directly at the facility and that experimentation is limited to a single test bench.
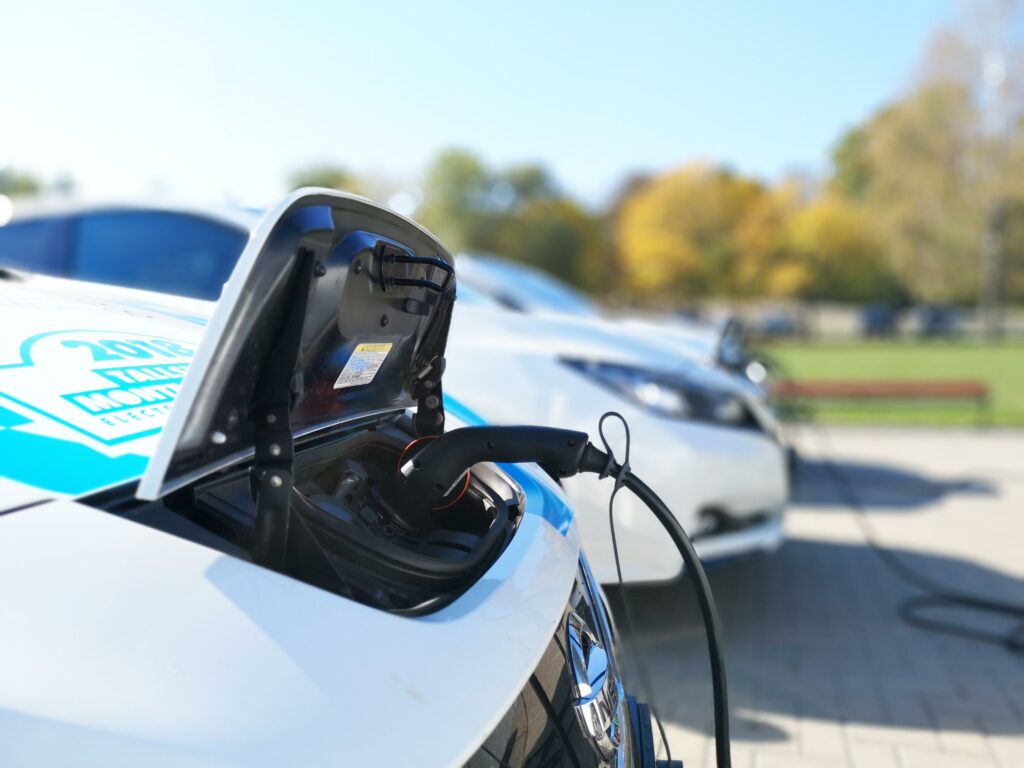
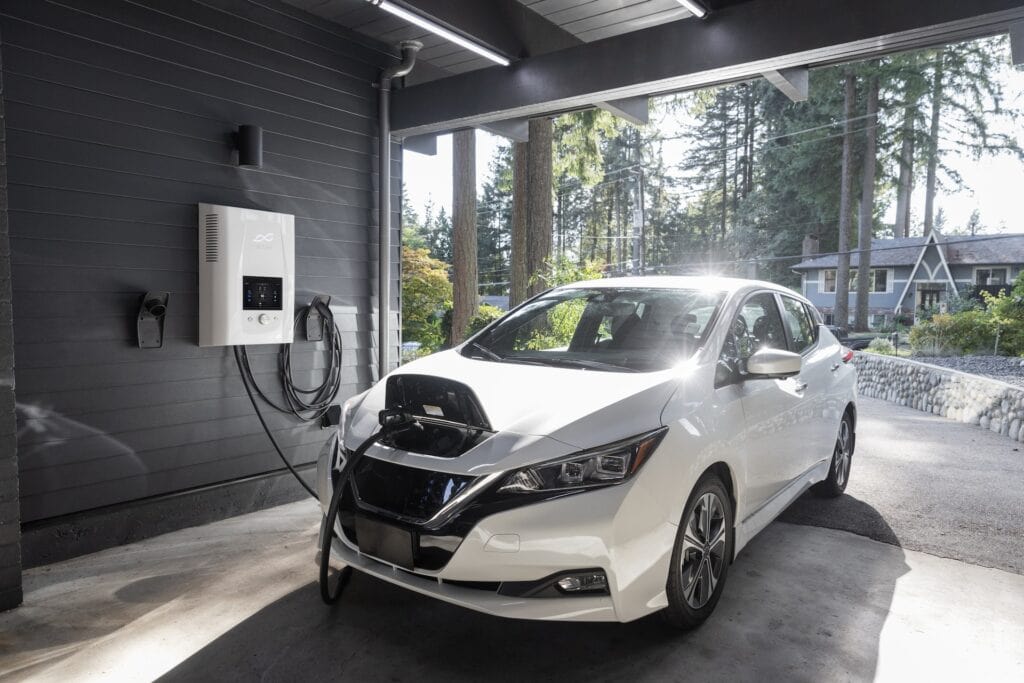
Revolutionising Battery Testing Technology
The FASTEST project aims to develop and validate a fast-track testing platform capable of delivering a strategy based on the Design of Experiments (DoE) and producing robust testing results by combining multi-scale and multi-physics virtual and physical testing. This approach will accelerate battery system R&D and enable the design of more reliable, safer, and longer-lasting battery systems. The project’s prototype fast-track hybrid testing platform promotes a new, holistic, interconnected approach. From a global test facility perspective, additional services—such as smart DoE algorithms, virtualised benches, and digital twin (DT) data—are incorporated into daily operations to reach new levels of efficiency.
Accelerating Battery R&D with Advanced Testing Methods
Throughout the project, the FASTEST consortium aims to develop the platform and its components up to Technology Readiness Level (TRL) 6. This includes optimal DoE strategies tailored to three distinct use cases—automotive, stationary, and off-road; support for two cell chemistries, 3b (NMC/Si-C) and 4 (solid-state with oxide polymer electrolyte); and the creation of a comprehensive set of physics-based and data-driven models capable of replacing physical characterisation experiments. Additionally, the project will establish an overarching Digital Twin architecture to manage information flows, culminating in a TRL 6-proven and integrated prototype of the hybrid testing platform.
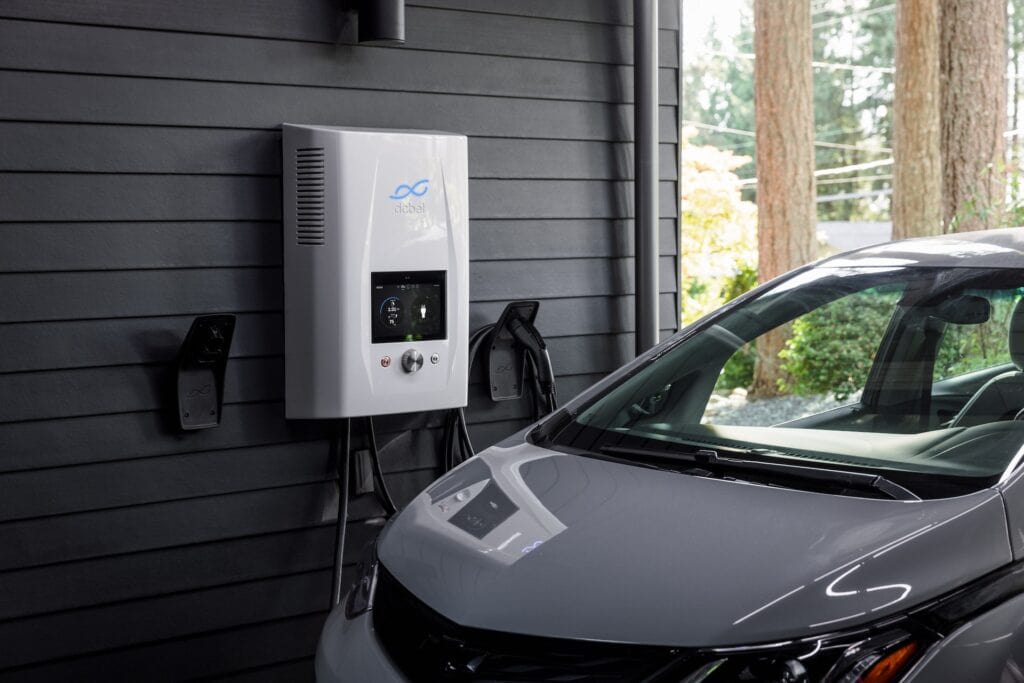
The project’s prototype of a fast-track hybrid testing platform introduces a holistic and interconnected approach to testing. From a global test facility perspective, additional services—such as smart DoE algorithms, virtualised benches, and digital twin (DT) data—are integrated into daily operations to achieve new levels of efficiency. The test facility management system retrieves all relevant information about test objects from available DT data. Before and throughout the test process, the system, together with the smart DoE algorithm service, will determine if the next measurement can be virtualised or requires execution on a physical test bench. Selected results are then reported to the DT for global access, ensuring maximum resource utilisation and seamless communication between test requesters, testing service suppliers, and other involved parties.
Within the FASTEST project, tailored DoE approaches will be developed for each use case to ensure that only experiments yield high-quality information are conducted. To minimise physical testing efforts, an intelligent combination of physical and virtual testing will be implemented, integrating DoE methodology guidelines and virtual Li-ion battery specifications. For this purpose, advanced heuristic algorithms and AI-driven methods will be developed to achieve an optimal distribution of experiments between virtual and physical testing, progressing from TRL 4 to TRL 6.
The work plan will advance the virtual testing platform from a partially validated concept with well-known components (TRL 3-4) to a fully integrated, TRL 6-proven prototype of the hybrid platform, tested across two cell chemistries and three use cases.
The project’s work on implementing a DT architecture to virtualise the battery system and its components will:
- Develop an adaptable and scalable ontology tailored to the battery systems development and testing domain, maximising precision and confidence in analyses. This approach leverages extensive, well-structured data, providing comprehensive behavioural insights validated against a reduced number of physical tests.
- Represent the battery system through interconnected virtual models of its components, systematically mapping all relevant development variables in an accessible format. This structure will enable seamless integration between different agnostic virtual models of each component and setting.
Ultimately, the development of the battery system DT will establish robust, organised data management for all components, supporting information management and interaction with the fast-track hybrid testing platform. This digital replica-based data management system will facilitate faster and more reliable product validation. The architecture’s implementation is expected to progress from TRL 4 to TRL 6; while the individual virtual models are established, the innovation lies in creating a data structure that accurately virtualises the battery system, develops tests, and facilitates comprehensive architecture integration and communication. This advancement will accelerate R&D in battery development, where such virtualisation has yet to be realised.
FASTEST will employ digitalisation approaches using compatible physics-based and data-driven models tailored for automotive, stationary energy storage, and off-road mobile devices, alongside an AI-powered toolchain. This will support the Digital Twin (DT) concept in assessing safety and reliability, addressing key challenges in battery modelling and testing.
The project will focus on developing accurate, rapid virtual models to replace performance, thermal, ageing, and mechanical testing at cell and module levels. Physics-based models will be validated (from TRL 4 to 5) across a wide operational range, and reduced-order modelling techniques will be applied to maintain accuracy while enhancing operational efficiency. These models will be updated to account for ageing, reaching a final TRL of 5. Data-driven models will complement this work, drawing on experimental data and results from enhanced physics-based models. Together, these approaches will reduce resource demands without compromising accuracy and offer valuable insights unique to physics-based information.
Additionally, FASTEST will work on virtualising critical battery safety and reliability experiments across cell-to-system levels as outlined by test standardisation groups. This will involve developing an AI-powered "multi-physics" toolchain based on various degradation modes and conditions over the battery’s lifetime. The toolchain will undergo integration and validation (TRL 5) through Failure Modes and Effects Analysis (FMEA) to verify functional safety across different battery system scenarios within a standardised test matrix.
FASTEST will ensure both the protection and exploitation of research outputs in commercial activities (e.g., patent licensing and service offerings for battery manufacturing industries) and non-commercial initiatives (e.g., policy recommendations and standardisation efforts). Additionally, the consortium is committed to publicly disseminating data, scientific findings, and other relevant knowledge through appropriate channels (Section 2.2).
The project’s Dissemination, Exploitation, and Communication (DEC) strategy will follow an Open Science (OS) approach, adhering to the principle “as open as possible and as closed as necessary.” This approach will also foster engagement with relevant stakeholder groups in defining requirements, identifying uptake challenges, and co-assessing the piloted technologies. Furthermore, the strategy aims to strengthen scientific cooperation by actively engaging with major EU initiatives, such as Batt4EU and Battery 2030+.